Navigating CalGEM Inspections: A Guide for Oil and Gas Companies
DB
Understanding CalGEM Inspections
California's Geologic Energy Management Division (CalGEM) is a critical regulatory body overseeing oil and gas operations within the state. For companies operating in this sector, navigating CalGEM inspections can be a complex process. This guide aims to demystify the inspection process and provide strategies for compliance.
CalGEM is responsible for ensuring that oil and gas operations are conducted safely and responsibly. This includes the oversight of environmental impacts, safety procedures, and operational compliance. Understanding these inspections is crucial for maintaining operational continuity and avoiding potential fines or shutdowns.
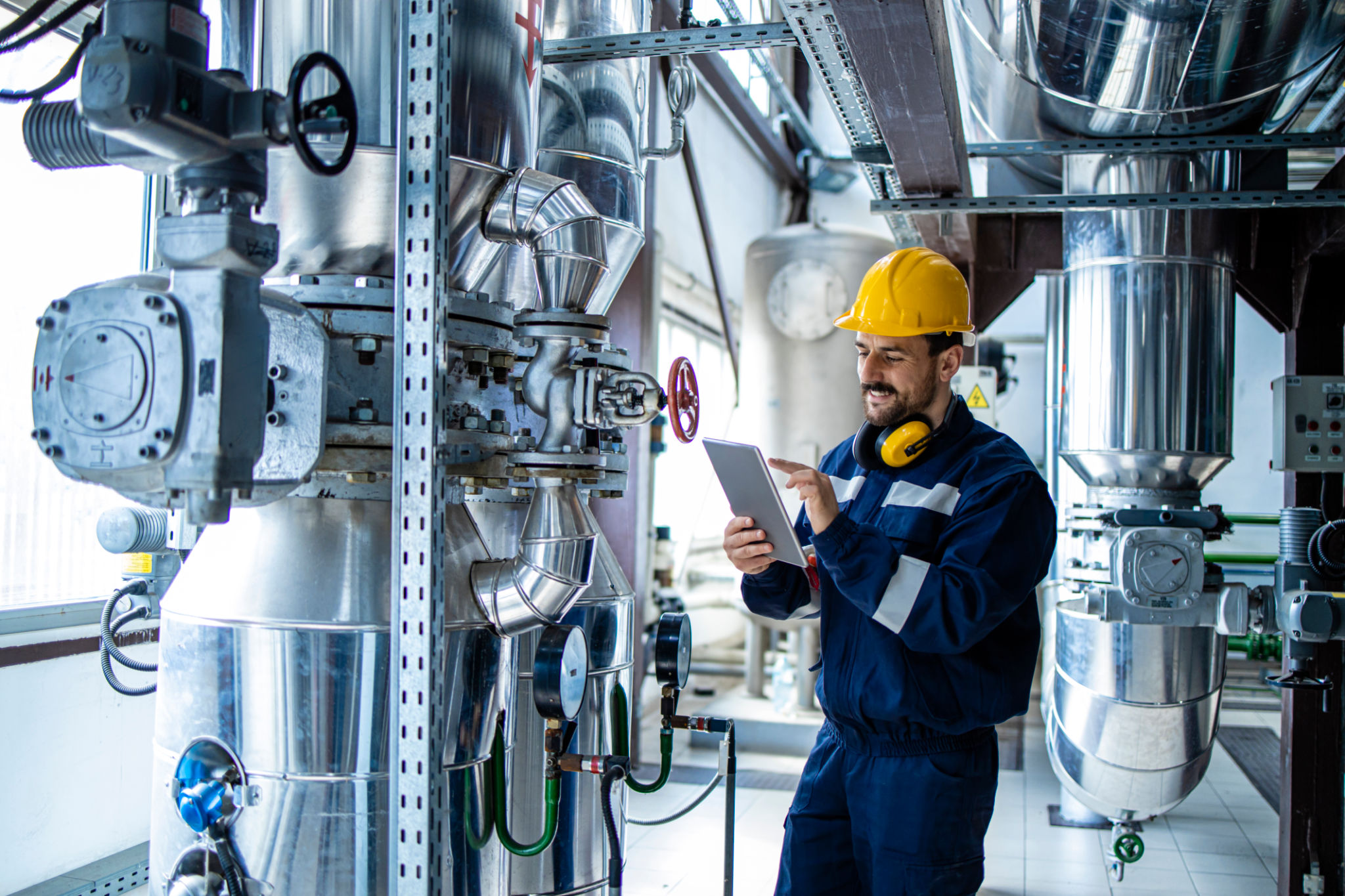
Preparing for an Inspection
Preparation is key to successfully navigating CalGEM inspections. Companies should have a comprehensive understanding of the regulations and ensure all documentation is up to date. Regular internal audits can help identify areas of non-compliance before an official inspection.
It's important to maintain clear records of all operations, including drilling activities, waste management, and safety protocols. Good record-keeping practices not only make inspections smoother but also demonstrate a company's commitment to compliance and safety.

The Inspection Process
During a CalGEM inspection, inspectors will evaluate various aspects of the operation. This includes site safety, environmental impact controls, and adherence to regulatory requirements. Inspections can be scheduled or unannounced, so companies should always be prepared.
Inspectors will typically conduct a site tour, review documentation, and interview staff about their roles and responsibilities. It's beneficial for companies to appoint a knowledgeable representative to liaise with inspectors, ensuring that any questions or concerns are promptly addressed.
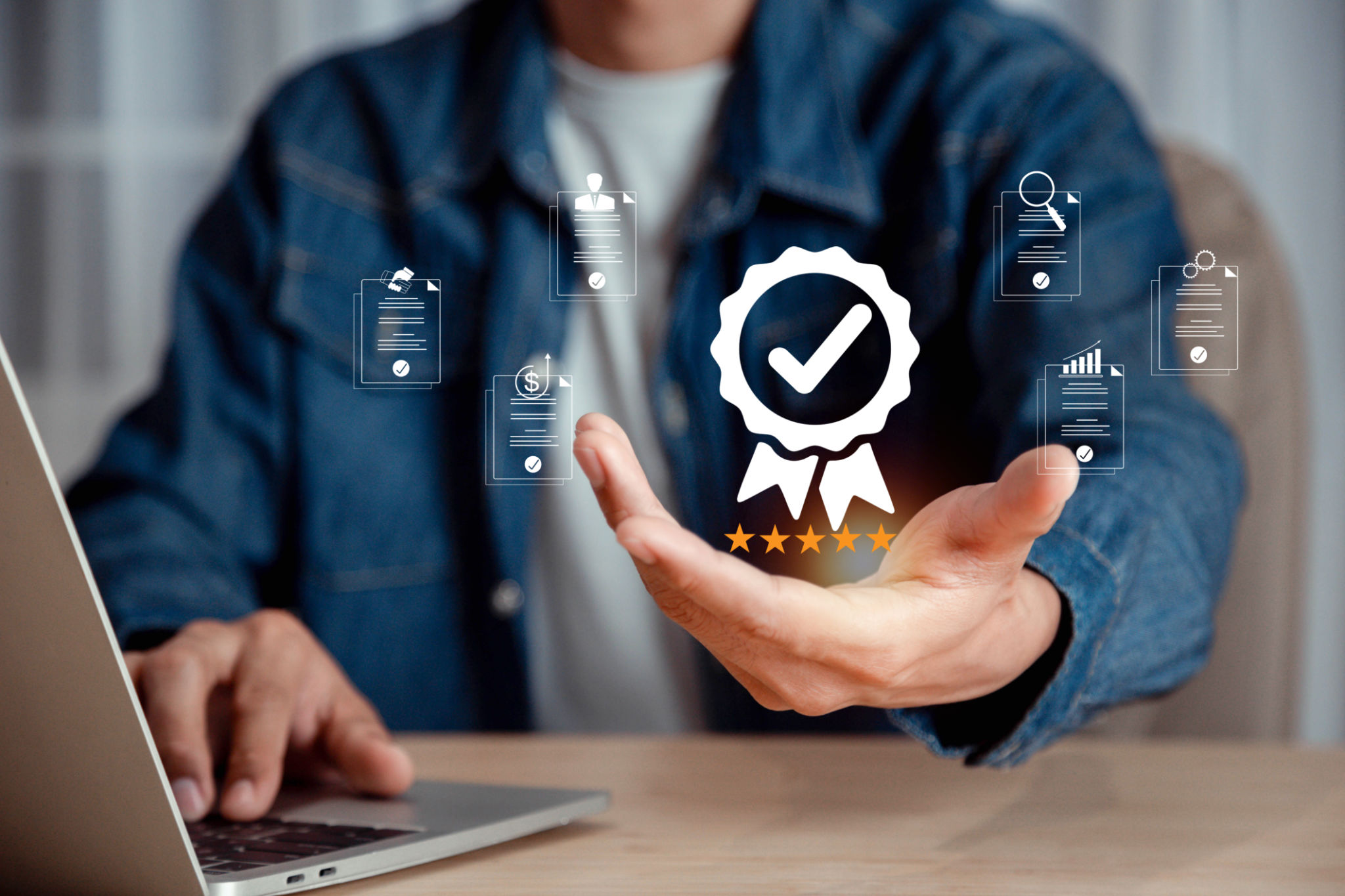
Common Compliance Challenges
Several common challenges can arise during CalGEM inspections. These include issues with environmental compliance, safety violations, and incomplete documentation. Companies should be proactive in identifying potential problem areas and addressing them before an inspection occurs.
Regular training and updates on regulatory changes can help staff stay informed and prepared. Investing in technology that aids in compliance monitoring can also prove beneficial in mitigating risks.
Post-Inspection Actions
After an inspection, companies will receive a report detailing any findings and required actions. It's crucial to address these promptly to avoid penalties or further regulatory action. Developing a corrective action plan can help ensure that all issues are resolved efficiently.
Communication with CalGEM is essential post-inspection. Engaging in open dialogue with inspectors can provide clarity on requirements and expectations, fostering a collaborative approach to compliance.
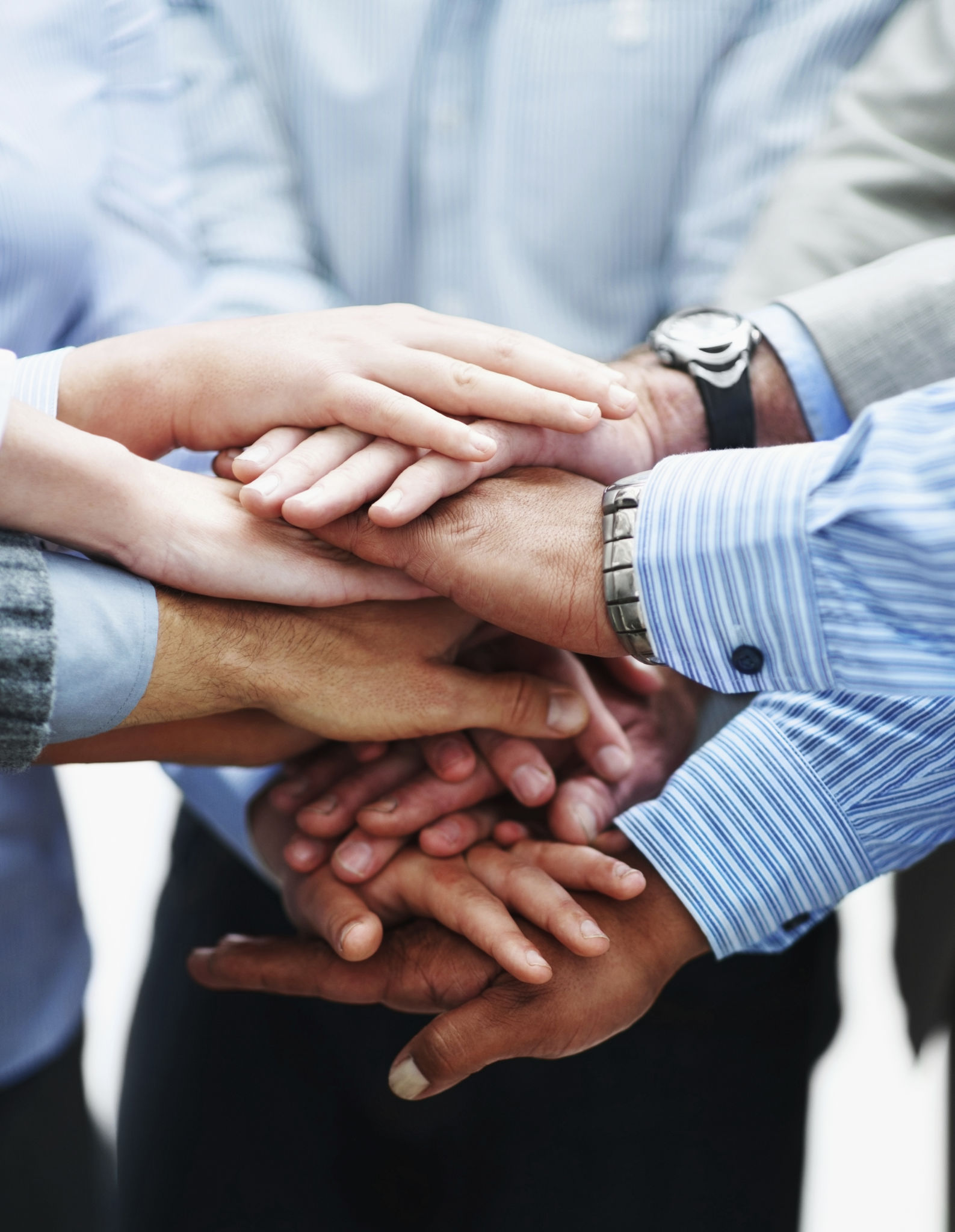
Continuous Improvement
Navigating CalGEM inspections is an ongoing process. Companies should strive for continuous improvement in their operations by regularly reviewing procedures and implementing best practices. This proactive approach not only aids in compliance but also enhances overall operational efficiency.
Ultimately, understanding and effectively managing CalGEM inspections can lead to improved safety standards, reduced environmental impact, and a stronger reputation within the industry.